the binder. The procedures follow those used for
hot-mix design (Marshall method), in general, with the
following modifications:
. Aggregates. Aggregates should be dried to a
moisture content expected during construction (up to a
maximum of 2 percent, by weight).
. Asphalt. Mix selected bitumen with the
aggregates, but at the temperature recommended for
field application. The aggregates remain at room
temperature.
. Curing. Before compaction, cure the mixture for
at least 12 hours in an oven set at 140°F ( + 5°).
l Cooling. After molding, cool the specimens to
room temperature in the molds. You must take care to
remove the specimens, undisturbed and undamaged,
from the molds.
. Testing. Heat the specimens in an oven to 100°
( + 2°) and test them in the Marshall machine. Heating
will normally take about 2 hours.
l Selection of the design amount of asphalt. The
asphalt contents at maximum density and maximum
stability, after averaging, are used as the design amount.
SURFACE AREA METHOD
OF MIX DESIGN
When laboratory equipment, except for sieve
analysis, is not available, the following formulas may
be used in place of laboratory procedures to determine
the necessary asphalt content:
1.
where:
P =
a
=
For asphalt cement:
P = 0.02a + 0.07b + 0.15c + 0.20d
percent (expressed as a whole number) of
asphalt material by weight of dry aggregate
percent (expressed as a whole number) of
mineral aggregate retained on the No. 50
sieve
percent (expressed as a whole number) of
mineral aggregate passing the No. 50 and
retained on the No. 100 sieve
percent (expressed as a whole number) of
mineral aggregate passing the No. 100 and
retained on the No. 200 sieve
d = percent (expressed as a whole number) of
mineral aggregate passing the No. 200 sieve
Absorptive aggregates, such as slag, limerock, vesicular
lava, and coral, will require additional asphalt.
2.
where:
P =
A =
B =
C =
Q1.
b =
c
=
17-22
For asphalt emulsion:
P = 0.05 A + 0.1 B +
percent (expressed as
0.5 C
a whole number) by
weight of asphalt emulsion, based on weight
of graded mineral aggregate
percent (expressed as a whole number) of
mineral aggregate retained on the No. 8 sieve
percent (expressed as a whole number) of
mineral aggregate passing the No. 8 sieve and
retained on the No. 200 sieve
percent (expressed as a whole number) of
mineral aggregate passing the No. 200 sieve
QUESTIONS
Your battalion has been tasked to replace a
5-inch-thick 2,000-square-yard reinforced
concrete parking lot located at a naval air facility
in northern Japan (extreme exposure). Your job
is to design a concrete mix and determine the
total quantities of materials needed to complete
the project. Based on the parameters listed below,
what is the (a) maximum size of the coarse
aggregate that you should use, (b) amount of
water (in gallons) needed for a 1-cubic-yard trial
batch (c) amount of sand (in pounds) needed for
a 1-cubic-yard trial batch (d) number of sacks of
Type IA cement needed for the project, and (e) the
amount (in tons) of coarse aggregate needed for
the project?
Average 28-day compressive strength
(based on flexural-design strength)
Fineness modulus of fine aggregate
Specific gravity of portland cement
Specific gravity offine aggregate
Specific gravity of coarse aggregate
Dry-rodded weight of coarse aggregate
Dry-rodded weight of fine aggregate
Slump
3,500 psi
2.6
3.15
2.75
2.65
110 lb/cu ft
100 lb/cu ft
2 in
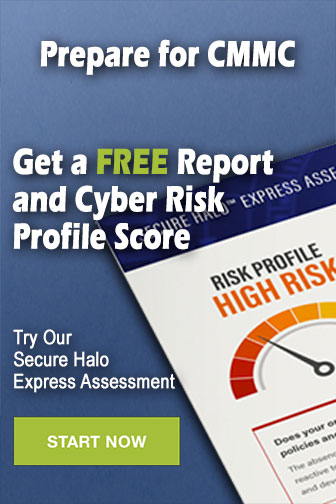