person will use the baseline noise measurements to
assess the noise and recommend modifications if
necessary. This is a complex task and may require
specialized acoustical instruments. If the ship does not
have access to a formal noise assessment, you should
assume personnel who work in noisy areas are at risk
and protect them as well as possible under the guidance
of this program.
In some cases, industrial hygienists may decide that
hearing protective devices do not give enough
protection in a particular location. They will then
analyze noise levels at that location from 84 dB
continuous or intermittent noise to 140 dB peak sound
pressure for impact or impulse noise. They will
determine the potential hazard and recommend
modifications in noise reduction or hearing protection
to reduce it. They will resurvey within 30 days after any
modification that might alter the intensity of noise and
recommend action based on the results.
In areas where there is a strong potential for hearing
damage, a medical officer or audiologist will conduct
hearing medical surveillance on personnel who work in
the areas. They will use their findings to decide if and
under what circumstances personnel may continue to
work there. They may recommend a reduction in noise,
better hearing protective equipment, or both.
It may not be necessary to apply all hearing
protection measures in every case, but qualified
professionals using approved methods should make that
decision. For example, personnel who sometimes enter
noise hazard areas may have to wear hearing protective
equipment, but they will not need to have their hearing
tested. At other times, noise may be intermittent and may
not require personnel to wear hearing protective
equipment. These waivers must be justified and
documented.
HEARING TESTS AND MEDICAL
EVALUATION
All personnel will receive a baseline hearing test
when they enter the Navy. The results will serve as a
reference for further testing as long as they are in the
Navy. Hearing tests done at military entrance stations
will not be used for this purpose.
Personnel who are assigned to duties in designated
noise hazardous areas or who operate noise hazardous
equipment will be included in the hearing conservation
program. An MDR will give these personnel a hearing
test annually for as long as they remain in a noise
hazardous environment and will enter the results in their
medical files. The MDR will give additional hearing
tests if anyone in the program develops hearing
problems.
PERSONAL HEARING PROTECTIVE
DEVICES
Personal hearing protective devices should reduce
noise to a level where it does no harm to hearing.
However, only an industrial hygienist or other
competent person can decide which device or
combination is suitable in each noise hazard situation.
Normally, the correct devices will have been selected
and they should be available to you whenever you enter
designated noise hazard areas. You should wear them at
all times when the noise sources are operating,
especially if you are subject to the noise of gun or missile
firing. When sound levels exceed 104 dB, you should
wear double protection; a combination of insert-type
and muff-type hearing protection devices.
LABELING HAZARDOUS NOISE AREAS
Label all hazardous noise areas and equipment that
produce hazardous noise with approved decals or labels.
The labels are NAVMED 62602, Hazardous Noise
Warning Decal (8 x 10-1/2), NS0105-LF-206-2605,
and NAVMED 6260/2A, Hazardous Noise Label (1 x
1-1/2), NSN0105-LF-21 2-6020. Normally, you should
post the outside of doors and hatches leading into a noise
hazardous area, but this does not include weather
surfaces. If a noise hazardous area has an entrance from
a weather deck post the warning on the inside of the
weather deck door or hatch. Do not label exteriors of
military combat equipment, but notify the personnel
who operate and maintain the equipment about any
noise hazards. All hands are expected to comply with
hazardous noise labels wherever they appear.
REDUCING NOISE
Most work to reduce or eliminate noise will be done
when the ship and its equipment are designed,
constructed, and tested, or following post-overhaul
baseline surveys. Any hazardous noise areas not
identified during those times are most likely due to
malfunctioning equipment. Other recommendations for
noise reduction may come from industrial hygienists or
other workplace inspections, such as zone, INSURV,
ISIC, or TYCOM. The CO should correct these
problems as soon as possible.
10-5
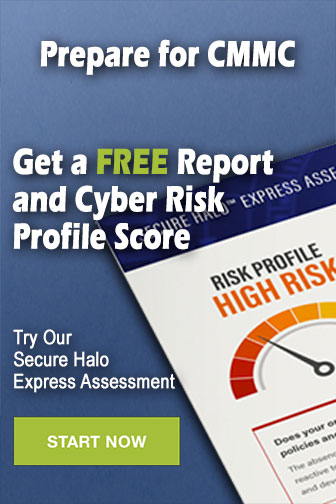