suspension. The manner in which the correction factors
are determined and applied to obtain corrected readings
can be found in ASTM D 422 and NAVFAC MO-330.
The corrected readings are used to determine the percent
passing and the particle sizes corresponding to each
reading.
As you know, the larger particles in a soil-water
suspension settle more rapidly than the smaller
particles; therefore, for each hydrometer reading, the
percent passing is the percentage of soil remaining in
suspension at the level at which the hydrometer
measures the density of the soil-water suspension. That
percentage, for each hydrometer reading, can be
calculated using the formulas given in NAVFAC
MO-330 or ASTM D 422. The particle sizes
corresponding to each of those percentages is calculated
on the basis of Stokes law, that relates the terminal
velocity of a free-falling sphere in a liquid to its
diameter. To calculate the sizes, use the formulas given
in ASTM D 422 or use the nomograph procedure
discussed in NAVFAC MO-330.
CONCRETE AND CONCRETE TESTING
As you learned in the EA3 TRAMAN, concrete is
one of the most economical, versatile, and universally
used construction materials. It is one of the few building
materials that can be produced directly on the jobsite to
meet specific requirements. In this section, you will
study the materials used to produce concrete and you
will further your knowledge of concrete testing.
COMPOSITION
Concrete is a synthetic construction material made
by mixing cement, fine aggregate, coarse aggregate, and
water together in proper proportions. The following
paragraphs discuss each of these materials:
Cement
Cement is a substance that hardens with time and
holds or entraps objects or particles in a definite
relationship to each other. For concrete, portland
cement is usually used. Portland cement is
manufactured by a standardized process consisting of
grinding limestone and clay, mixing them in
proportions, heating the mixture to a high temperature
to form clinkers, and then pulverizing the clinkers so
that 95 percent of the material will pass through a No.
200 sieve. The following paragraphs describe the
various types of Portland cement:
. TYPE I. Normal portland cement is an
all-purpose type used to make ordinary concrete
pavements, buildings, bridges, masonry units, and the
like.
. TYPE II. Modified portland cement is a type
that generates less heat during the curing process than
Type I. The hydration process generates heat that, in a
large mass of concrete, can become high enough to
affect the concrete adversely. Type II is also more
sulphur-resistant than Type I. Sulphur exists in water or
soil having a high alkali content and has an adverse
effect on the concrete.
. TYPE III. High-early-strength portland
cement, as the name suggests, is used where a high
strength is needed quickly. That maybe due to a demand
for early use, or in cold-weather construction to reduce
the period of protection against low or freezing
temperatures.
. TYPE IV. Low-heat portland cement has the
heat-resistant quality of Type II, but to a higher degree.
It develops strength at a slower rate than Type I but helps
prevent the development of high temperatures in the
structure with the attendant danger of thermal cracking
upon later cooling.
. TYPE V. Sulphate-resistant portland cement
has a higher degree of sulphate resistance than Type II
and is for use where high sulphate resistance is desired.
Other types of cements maybe variations of the five
types above or may be special types. Some of these types
are as follows:
. TYPE IS. Portland blast-furnace slag cement
uses granulated slag, which is rapidly chilled or
quenched from its molten state in water, steam, or air.
The slag (from 25 to 65 percent of the total weight of
the cement) is interground with cement clinker. This
cement is for general use in concrete construction.
. TYPE IP. Pozzolan cement uses a mixture of
from 15 to 40 percent of pozzolan with the cement
clinker. Pozzolan is a siliceous or siliceous and
aluminous material, such as fly ash, volcanic ash,
diatomaceous earth, or calcined shale. The strength of
concrete made with pozzolanic cements is not as great
as concrete made with the same amount of Portland
cement, but its workability may be better for some uses.
. AIR-ENTRAINED CEMENT. Concrete made
with air-entrained cement is resistant to severe frost
action and to salts used for ice and snow removal. It is
produced by adding air-releasing materials to the
13-19
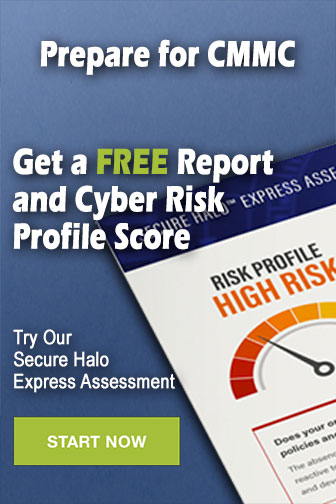