appoint a controlled material petty officer (CMPO) to
handle these responsibilities in the work center. After
training, that person will inspect, segregate, stow, and
issue controlled material in the work center.
SHOP CRAFTSMEN
Shop craftsmen are not normally trained in specific
QA functions as are the key QA people. Still, they must
do their work under QA guidelines if they apply. They
will work closely with their shop supervisors and QA
inspectors to be sure the work is done according to QA
guidelines and procedures.
QUALITY ASSURANCE TRAINING
AND QUALIFICATION
The following paragraphs cover the responsibilities
for training as well as training and qualifications of key
QA personnel and others with less specific QA
responsibilities.
THE QUALITY ASSURANCE OFFICER
The QAO coordinates the ships QA training
program and makes sure it is an integral part of the ships
overall training program. The QAO qualifies key
personnel to serve in their collateral duty QA positions.
THE DIVISION OFFICER
Division officers ensure that their divisional
personnel are trained and qualified in the QA processes
and that they maintain those qualifications.
QUALITY ASSURANCE COORDINATORS
QACs are senior petty officers who have been
properly qualified according to the QA manual. They
help train all SQCIs and CMPOs and ensure their
recertification when necessary. QACs also administer
written examinations to prospective SQCIs and to
SQCIs who require recertification.
SHIP QUALITY CONTROL INSPECTORS
The QAO interviews SQCIs to determine general
knowledge of QA and attitude toward the QA discipline.
If they are accepted, the QAO and QAC will qualify
them in the requirements set forth in the QA manual and
the commands QC requirements. Qualifications
include formal instruction and OJT, a written
examination on general requirements, and may include
a practical examination on specific requirements in the
SQCIs specialty and in knowledge of records, reports,
and filing. The shop qualification program course for
SQCIs will answer this requirement.
CONTROLLED MATERIAL PETTY
OFFICERS
On ships with level I systems, the QAO interviews
E-4 and E-5 petty officers as prospective CMPOs. For
those who pass the interviews, the QAO and QAC will
train and qualify them as CMPOs. This includes written
tests to be sure they are familiar with controlled material
requirements as outlined in the QA manual and material
identification control (MIC) manual.
OPERATION OF A QUALITY
ASSURANCE PROGRAM
An effective, ongoing QA program is an all-hands
effort. It takes the cooperation of all shop personnel to
make the program work. As a key group supervisor, you
will be responsible for keeping the program rolling.
PERSONNEL ORIENTATION
One of your first steps is to get the support of your
personnel. Some of them will oppose the program but
that is usually true of any new approach. The best way
to overcome opposition is to show them how an
effective QA program will help them personally.
Explain how it will eliminate or reduce premature
failures in repaired units and introduce high-reliability
repairs. These improvements will reduce the workload,
lower frustration, and improve the shops or work
groups reputation.
QUALITY ASSURANCE TERMS AND
DEFINITIONS
You need to talk to your personnel about QA in
terms they understand. Use words and phrases that
suggest quality, and relate them to familiar programs.
This should improve the clarity in your communication
with them about QA. To do this, you need to understand
the terms frequently used throughout the QA program.
Each TYCOMs QA manual and MIL-STD-109 has a
complete list of these terms. We have listed the ones used
most frequently in the next paragraphs, and we will
discuss the more important ones in more detail
following the list.
Quality assurance: A system that ensures that
materials, data, supplies, and services conform to
8-4
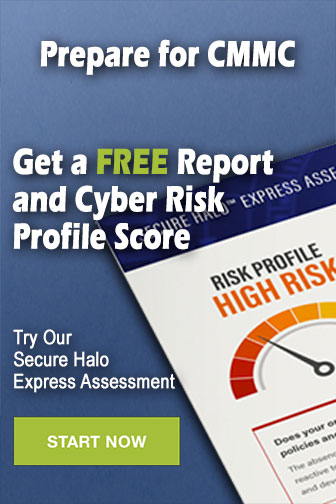