Fine aggregate grading limits are specified by the
American Society for Testing and Materials; however,
since many gradings of fine aggregate can produce a
good quality concrete, the engineer should compute the
fineness modulus of the aggregate and compare it to the
specified concrete class requirements.
The fineness modulus is an empirical factor that
gives a relative measure of the proportions of fine and
coarse particles in an aggregate. It is a value widely used
to indicate the relative fineness or coarseness of a fine
aggregate. To obtain the fineness modulus, sieve a
500-gram sample of sand through a series of sieves
(Nos. 4, 8, 16, 30, 50, and 100). Convert the weight
retained on each sieve into a cumulative percentage
retained, starting with the No. 4 sieve. Divide the sum
of the six percentages by 100. The resulting answer is
the fineness modulus. Typical fineness modulus values
are as follows:
Fine sand
= 2.20 to 2.60
Medium sand = 2.60 to 2.90
Coarse sand
= 2.90 to 3.20
TESTS FOR SOUNDNESS. Soundness is the
property of aggregate to resist disintegration when
subjected to freezing and thawing. Two methods are
used to test for soundness. In the freeze-thaw test
method (ASTM C 666), concrete specimens, made with
the aggregate in question, are placed in water and then
subjected to alternate cycles of freezing and thawing. An
alternate method, requiring considerably less equipment
and time, is the salt test. This procedure involves
solutions of special salts (sodium sulfate or magnesium
sulfate) in which the aggregate is immersed and
saturated. The crystals of these salts are permitted to
grow that creates a disruptive force similar to freezing
water. You can find the procedures to perform the salt
test in ASTM C 88 and in NAVFAC MO-330.
TESTS FOR IMPURITIES. The quality of
aggregate is another important consideration. The
presence of organic material, excessive quantities of silt
or clay and shale, or other water-absorbing particles can
be detrimental to the concrete strength, watertightness,
and durability. Tables showing the recommended limits
of deleterious materials in fine and coarse aggregate can
be found in NAVFAC MO-330.
Test for Material Finer Than No. 200 Sieve. The
extremely fine mineral material (clay, silt, dust, or loam)
occurring in most aggregates can affect concrete in two
ways. The added surface area of the fine particles picks
up the cement paste and reduces the amount available
to bind and hold the aggregate. The small particles also
tend to float up to the surface when the concrete is
finished (especially when wet mixes are used). That
results in a surface covered by hairline cracks and a
tendency for the fines to dust off when dry. For some
purposes a small amount of fine material may improve
workability; however, amounts in excess of 3 to 5
percent of the total weight of the aggregate are generally
considered harmful to the concrete.
The specific procedures that you should follow
when testing for these fine materials can be found in
ASTM C 117 and in NAVFAC MO-330. Briefly, you
oven-dry and weigh a sample of the aggregate. Then the
dried sample is brought to suspension in water and is
carefully poured through a nest of sieves (No. 16 and
No. 200) until the wash water is clear. Finally, the
material remaining on the sieves is oven-dried and
weighed. The percent of material finer than the No. 200
sieve is then calculated using the following formula:
Where:
P =
wd =
Wdw =
Percentage of fines
original dry weight of sample
dry weight after washing
The method described above is accurate, but
time-consuming. When time is critical and less accurate
results are acceptable, you can place a 1,000-gram
sample into a quart mason jar to a depth of about 2
inches. Then fill the jar three-fourths full of water, shake
the mixture vigorously, and allow it to stand for 1 hour.
The silt and clay will form a layer at the top of the sand.
If the layer is more than 1/8 inch thick, the material has
more than 3 percent fines and should be washed before
using.
Test for Clay Lumps and Friable Particles. This
test is performed on the material remaining after you
determine the material finer than the No. 200 sieve. The
size of samples needed and the specific test procedures
that you should use are in ASTM C 142 or in NAVFAC
MO-330. Spread the sample in a thin layer on the bottom
of a flat pan and cover it with distilled water. After about
24 hours, you break up all particles by crushing them
between the fingers. Next, you remove the broken clay
lumps and friable particles by wet sieving over the
appropriate one of the following sieves: aggregateNo.
20; No. 4 to 3/8 inchNo. 8; over 3/8 inchNo. 4.
13-23
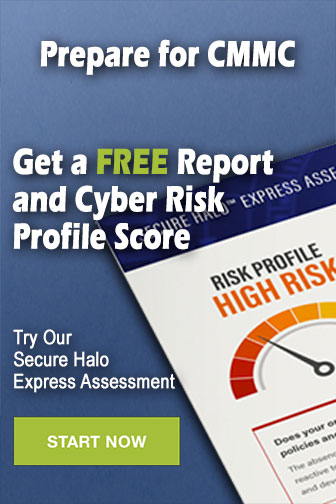