3. Next, you place a water-absorption cone (fig.
13-18) large end down on a smooth surface and fill it
loosely with the aggregate. Then lightly tamp the
surface of the aggregate 25 times with the metal
tamper.
4. Lift the cone vertically from the sand and
observe the action of the sample. If it retains its
conical shape, free moisture is present and continued
drying (Step 2) followed by repeated tamping (Step 3)
is required. If the sample slumps slightly, the fine
aggregate has reached the desired SSD condition.
5. Weigh exactly 500 grams of the SSD sample
and place it in a partially water-filled pycnometer
top-and-jar assembly (fig. 13-19). Fill the jar with
additional water to approximately 90 percent of its
capacity.
6. Agitate the sample in the pycnometer
assembly to remove any entrapped air, adjust the
water temperature to 23°C, and fill the pycnometer to
its calibrated capacity. Then weigh the filled
pycnometer to the nearest 0.1 gram and record the
weight.
7. Remove the sample from the pycnometer and
dry it to a constant weight at 110°C. Then cool the
sample in air for about 1 hour and weigh it. Record
this weight to the nearest 0.1 gram.
8. Determine the weight of the pycnometer filled
to its calibrated capacity with water at 23° + 1.7°C.
Record this weight.
9. You can now calculate the specific gravity of
the SSD fine aggregate and the percentage of
absorption by using the following formulas:
SSD bulk specific gravity = 500
B + 500 C
And:
500 A
% absorption = ( A ) x 100
Where:
A = weight of the oven-dried specimen in air (in
grams)
B = weight of pycnometer filled with water (in
grams)
C = weight of pycnometer, sample, and water (in
grams)
Surface Moisture (ASTM C 70 and ASTM C
566). A summary of the ASTM procedures used to
determine the total moisture content and the
Figure 13-18.Water-absorption cone and
tamper.
Figure 13-19.Pycnometer top-and-jar
assembly.
percentage of surface moisture in either fine or coarse
aggregate are as follows:
1. Secure and weigh a sample of the aggregate
that is representative of the moisture content of the
material being tested.
2. Dry the sample to a constant weight at 110°C.
You should take care to avoid loss of material during
testing. The sample is thoroughly dry when further
13-26
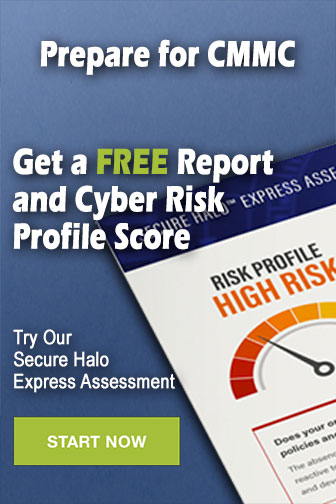